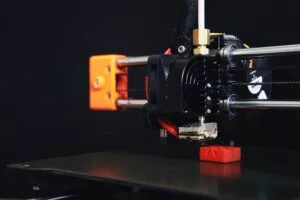
3D Printers – An Overview and Buying Guide
3D printing is certainly not a new phenomenon but having one at home still feels novel and exciting. Being able to create three-dimensional plastic objects at home has been revolutionary for many crafty creators, tabletop tacticians, ingenious engineers and more.
Getting started with 3D printing
The various types of 3D printing technologies all create real-world three-dimensional objects from digital models via the addition of material. These processes are able to produce novel structures that other manufacturing techniques cannot. Usually, the 3D printing process looks like this:
- Start with a digital 3D model – whether you create one yourself in 3D modeling software, or finding one online.
- Using a preferred Slicer program like Cura, generate instructions for the printer.
- Run your machine according to its instructions. Keep an eye or ear out for misprints and malfunctions.
- Let the print cool or cure completely.
- Post-process it so it looks and functions the way you like. This can involve cleaning up material, assembly of different printed parts, and painting.
The two main kinds of 3D printing
There are two main categories of Printer available on the commercial market in 2023. Those are:
Fused Deposition Modeling or Fused Filament Fabrication
These might be what you are picturing when we talk about 3D printers. These 3D printers push heated thermoplastic filament through a moving nozzle, building your programmed object up layer by layer. This form of printing can be generally fast, cheap, and inexpensive, ultimately depending on your printer and the exact material you are using for your prints. However, there is a margin for error, and this process can be sloppy
Stereolithography 3D printers
Some other printers use a thermosetting plastic, which harden after curing, taking on a new molecular form and remaining solid after the process is complete. Stereolithography (commonly abbreviated to SLA) 3D printers use a thermosetting resin, which is hit with a laser to cure the resin into a hardened plastic. SLA printing is capable of better resolution and accuracy than their FDM counterparts, and are capable of truly smooth surfaces, making SLA the go-to for users who need their components to have a specific texture, shape, or strong internal strength.
The different printer styles
The different ways that a printer can move and place filament or resin often define the use and care of these machines. We have broken down these styles of 3D printer, starting with the FDM printers.
Bedslinger / i3 style printers
Many of the smaller, less expensive 3D printers available follow this line of design, where the print-bed moves along the Y-axis, and the nozzles move along the X- and Z-axis. This system is ultimately simplistic in maintenance and design, with fewer moving parts, more exposed components, and a general cheaper assembly.
There are disadvantages specific to this kind of 3D printer, however. Movement of the bed, especially at higher velocities, causes a “ringing” effect, warping the layers you’ve laid down. Because of this, and the fact that this effect manifests in more pronounced ways with heavier print beds, bedslingers are better suited for hobbyist use than professional use.
Delta
Delta printers are a different beast entirely. Delta printers are based upon a triangular type of design, with the extruder attached to three different arms, each arm attached attached to its own vertical bar. Hard to visualize? I don’t blame you.
Because of this construction, Delta style printers excel in fast-printing, capable or getting perfect results at high speeds. The flip side is these printers are harder to troubleshoot, calibrate, or repair yourself. Plus, the kinematics of these printers mean resolution is not uniform, as the arms will be able to more accurately replicate fine detail closer to the centre than the edges.
Box-styled / Z-bed printers
Similar to bedslinger printers, Box-styled printers or Z-bed printers let the print bed get in on the movement, with the print bed moving on the Z-axis, or moving up and down, while the printhead moves along the X/Y axis. These printers offer stability and maintain a strong print quality when printing quickly. However, for these advantages, there are disadvantages: they are far more complex than bedslingers (more comparable in difficulty to troubleshoot / repair as a Delta printer) and are more expensive too. Also, they are boxy, and typically take up more space comparatively too.
Resin:
Resin printers use entirely different processes than their FDM counterparts to create 3D models. Resin printers utilize light, typically in the UV-range of the spectrum, to chemically turn the resin into solid plastic. There are two main form of resin printers, separated by how light is applied to the resin.
Digital Light Processing / DLP
Digital Light Processing uses UV light to cure resin, projecting light to cure an entire layer all at once. By utilizing digital micromirror devices, or DMD’s, the printer is able to “mask”, able to reflect the light either away from the resin, or towards a particular point in the resin, allowing for the light to very-accurately reproduce the layer. The benefit of this type of printer is they are typically faster than SLA machines, but struggle printing large items without warping, and also do not deal with the resin smell that well.
Stereolithography
In a similar process to Digital Light Processing machines, Stereolithography 3D printers also use a laser to cure resin into a hard plastic, but the main difference being how they use that light. SLA printers often have a laser that moves to make the image of each layer, either running underneath the resin vat or above it. SLA printers, because of their more precise controls, are more accurate in detail than their DLP counterparts.
Material choices
The properties you want from a 3D printed object rely on the material more than the printer – however the print quality itself often depends on how well equipped the printer is to print with that material. Familiarizing yourself with the materials of 3D printing is crucial
Common name | Scientific name | Qualities | Applications | Notes | Examples |
ABS | Acrylonitrile butadiene styrene | Tough, durable, and resistant to heat and impact – just like Lego, which are made from this material. | Functional prototypes | Requires both a heated bed and ventilation for successful printing | |
HIPS | High-impact polystyrene | Soluble support material combined with ABS printing Dissolves in the chemical limonene | Support material | Often used as a support material with ABS since it dissolves so easily. | |
PETG | Polyethylene terephthalate glycol | Resistant to both humidity and chemicals Lower printing temps | Waterproof applications | Offers sturdiness, smoothness, and water resistance. | |
PLA | Polylactic Acid | Easiest materrial to print on FDM printers
| Concept models | One of the most common types available, for a reason | |
PVA | Polyvinyl Alcohol | Water-soluble | Support materials | This material will dissolve in water. | |
TPU | Thermoplastic polyurethane | Impact resistant Highly flexible | Flexible plastic items and prototypes | This rubber-like material is capable of producing |
Resins
Resins are much different from filaments. While different kinds of filaments are different materials entirely, different kinds of resins are different formulations, which vary between brands and product lines.
You will likely receive a sample resin with the purchase of a resin 3D printer. Once this runs out, it is a safe bet to stick with the same brand of resin if the results from your first prints met your expectations.
Standard Resin
A standard resin just means it will be decent for general use, with no particular areas the resin excels in. Eco-resins generally fall under the umbrella of Standard Resin, which offer less odour and a generally more ecologically friendly than other kinds of reins.
EX: Flashforge Standard, Anycubic Eco
Water-Washable Resin
The washing-process of resin 3D printing, where prior to curing you remove any excess resin from the print, is not a very fun or user-friendly process. One thing that makes it just that much less user-friendly is that most resins require the use of alcohol during this process, but water-washable resins are an exception. These, as their name suggests, do not require alcohol, so the process is more convenient and cheaper too. However, these resins are not as strong and can be brittle, so they are not as structurally sound. They also can take longer to make.
Tough Resins
If you want to print functional parts in machinery and tech, tough resins are the place to look. Most 3D printer materials available do not have the structural strength to depend on in parts for machinery or construction. However Tough Resins do provide that kind of structural strength needed for industrial settings where parts and other components might be needed to spec regularly. However, since tough resins are designed for industrial use, they are not great to use at home. Not only do they produce a real strong odour during the printing process, but the resin itself can be quite expensive.
EX: ANYCUBIC Tough 3D Printer Resin
Draft Resin
Or sometimes called Rapid Resin, is resin designed for quick printing, perfect for prototyping or inpatient printers. Draft resin is formulated to have faster curing period, reducing the total amount of time you will need to complete a print. Since each layer takes less time cure and be completed, overall you can really notice a difference in how long it takes to print with a draft resin.
Flexible Resin
Flexible Resins are a great choice if you need your prints to have a rubber-like flexibility while still offering strong durability. These Flexible Resins are typically rated with a Shore hardness rating of 80A.
While certain projects are essential with Flexible resins, there are certain disadvantages with the current market for them. Few colour options are offered, limiting aesthetic choices with flexible resins. Also, the odours generated when printing is comparable to that of tough resins, which will make use indoors generally unpleasant.
EX: Siraya Tech Tenacious Flexible Resin
8K Resin
Some Resin printers may offer resolution as fine as 8K, and so naturally, resins for these machines are available too. While they will not necessarily make your prints on a 4K printer or printer with less resolution print better than other resins, these high-quality resins will be an optimal material for a high end unit and will work fine with most printer regardless.
EX: Phrozen 8K Resin
What to look at when shopping for a 3D printer
Before you start your search, narrow down your options by thinking about the factors below.
Type of prints you will make – The very first thing you should do when considering buying a 3D printer is to really consider what you want to create with the 3D printer. Think critically about the qualities of the prints you want – what types of objects do you want to print? What is the range of size you will want to print? What materials, or qualities of materials, do you want to print with? How long should a print take before completion? Ultimately, this will guide you towards certain kinds of printers, that can handle the size, shape, printer material, and pace that your printer will need.
Ease-of-use / Accessibility – Are you a 3D printer newb? Or are you an enthusiast looking to round out your array of printers for a big project? Not all printers are accessible to newcomers, and some just work by themselves, loaded with sensors and automated processes.
Price – 3D printers vary in price a lot. You can buy cheaper Bedslinging models for around $300, and high-performance resin and FDM printers alike can creep up into thousands. The higher end units – models like the Ultimaker S5 and the Formlabs Form 3 – offer high-end printing and options, that make sense for professional workspaces where the printers will always be buzzing, and make less sense for hobbyists.
The components of a 3D printer
Now that you have figured out some of the things you will need in your 3D printer, you can start thinking about individual components – specific things you need for optimal prints, handy things you do not want to do without, quality of life improvements that intrigue you. Here are some of the key components of a 3D printer that can define the experience printing certain prints with your printer.
Build volume
The build-volume of a 3D printer refers to the size of print it can produce at one time. Build volume is influenced by the size of the printer overall, and is usually described through the classic length by width by height measurements, where the printer can only print objects within those dimensions.
Build-volume can be quite limiting on cheaper units, but if your use is to create small toys or objects with your printer, than a smaller unit can be amply sized for your use.
The print-bed design and features
The print-bed is the component of a 3D printer that may seem least interesting, but also can be one of the most important components for assuring quality in the printing process. Many printers rely on the print-bed for the prints to adhere to, and some even rely on the print-bed to move.
The print-bed needs to have some sort of adhesion, so the 3D-printed item can be secure and be printed upon, but still easily come off the surface when the printing job is complete. Common materials for printbed include glass, PEI sheets, and adhesive tapes. However, these materials have different advantages and disadvantages. Textured glass is harder to clean for example, but smooth glass can struggle nailing that first layer, for example.
Filament compatibility
While we have talked about the differences between filament and resin, we have not dived in as much regarding the differences within filaments and resins.
Not all materials you can 3D print with will work with every printer, due to different mechanical requirements certain materials need. Almost all consumer grade printers are compatible with PLA, ABS and PETG.
According to 3dsolved.com, materials like Nylon, Polycarbonate and TPU can be printable on many different consumer machines, but might need upgrades, including swapping Bowden extruders to Direct Drive extruders, getting a hot-end with one that can reach higher temperatures, or getting enclosure for the printer to control the ambient temperature of the printing space.
Double checking the temperature that a filament melts at and any other recommendations relating to a new material you want to print will keep the process smooth.
Extruder
The extruder is the component of a Fused Deposition Modeling (FDM) that applies the filament in a liquid state onto the design. Most desktop 3D printers available have a standard nozzle size of 0.4mm, but the sizes of these nozzles do vary.
There are different types of extruders available, however knowing more about the construction of the extruder is helpful for illustrating the differences.
Direct extruders are attached to the hot end of the nozzle, which works very well at printing flexible materials, where Bowden extruders have a tube to link the hot end to the extruder body, which move material more quickly and can lead to faster prints.
Some printers now include dual-extruders, that enable simultaneous printing of two materials simultaneously, allowing for multi-coloured prints and the use of supporting materials during the process.
Enclosure
Working with certain materials, certain printers, or working on certain applications will require certain conditions. While PLA sets fine without any special precautions, some materials, like ABS are finicky when it comes to temperature of the air around them, and some SLA printers can produce obnoxious and even toxic fumes during the curing process.
If either material is something you may want to work with, we recommend looking for a 3D printer with an enclosure. While most SLA’s include enclosures standard, this might be harder to shop for if you want a FDM printer in particular.
Cooling fans / Filtration systems
While keeping the air warm around a print can be beneficial, so can cooling down warm components or moving air out of the unit. Especially with resin machines, the fumes can be unpleasant and even mildly toxic, so it’s a good idea to think about filtration or ventilation to ensure that your 3d printing space stays livable.
The best inexpensive printer
Creality Ender-3 V2
For many, the Creality Ender-3 V2 is the place to start if you are looking to get into the worlds of 3D printing, and for good reason. It’s cheap, small, and easy to get the hand of while learning the ins and outs. It also works well for a FDM printer in creating prints, although the smaller build volume does limit it in these categories.
Contributing to the Creality Ender 3’s price is the simplicity of this unit. This 3D printer will arrive at your home as a kit, requiring some assembly which should take a matter of hours, which is worth keeping in mind before purchasing. The instructions have some concerns (small, somewhat misleading diagrams, lack of troubleshooting help) but all the tools needed for assembly are included. We recommend you supplement these instructions with YouTube videos.
The Ender 3 is open-frame bedslinger printer, with a skeleton easily able to fit on a corner desk or table, measuring 62 x 47.5 x 47 centimeters (HWD) and weighs 17 pounds, or 7.7 kg. The Ender 3 has a Print Size of 220 x 220 x 250mm as result of this size. The printing components are elevated by two beams that rise alongside the base of the unit, along which the horizontal bar slides up and down.
Since this is a bedslinger-style printer, the print-bed is incredibly important. The print-bed on the Ender 3 V2 consists of a Carborundum Glass Platform, which provides a textured base that improves adhesion of the first layer. Unfortunately, there is no auto-levelling feature included, and while the manual leveling not an issue like some other cheaper 3D printers, it can still prove difficult to dial in exactly, and might requires some trial and error when you are printing.
The Ender 3 V2 features a manual filament feeding mechanism for improved feeding and purging of the filament, however loading of the filament is somewhat of a problem for the Ender 3. The hole used to load the filament is small, and located right beside the leadscrew, meaning it is not the most accessible nor fastest layout for the extruder. This printer supports PLA, ABS, PETG and PTU materials, which covers a large number of the more popular filaments available.
The controls of this unit, which sit at the bottom right of the base, features a 4.3 Inch Color LCD Screen and a control knob that cycles through the choices. The brains of this printer is a 4.2.2 32-bit Silent mainboard, which is as precise and dependable as it is quiet. The unit is powered by a UL Certified Meanwell Power Supply. The base has a slot for a microSD card, as well as a micro-USB port. The user interface via the control knob is not the slickest UI, but the only real complaint is the reliance of shorthand on the interface, which might take a second to figure out which filename you are looking at.
The Creality Ender includes its own printing software called Creality Slicer, which is downloaded on an included SD card. If you are familiar with the slicer software Cura, Creality Slicer definitely bares a resemblance to it.
Additionally, there are a handful of features that we would feel we are doing a disservice by not mentioning. A host of settings improve the printing experience, including the ever-handy Print Resume Function, tensioner knobs on the X/Y axis, and a “toolbox” compartment in the base lets you store components, tools, and other things you may need.
The Creality Ender 3 is ultimately an inexpensive 3D printer that can produces carefully-crafted prints, but where the Creality Ender 3 really excels in teaching newcomers to 3D printing the ins-and-outs of the hobby. While assembly might be off putting to beginners, it should be seen as an opportunity to let users get familiar with all the components individually through building the unit. While the disappointing instructions may not aid in this, the Ender 3 is a well-documented 3D printer due to its popularity and will have setup and troubleshooting tips readily available online. However, that is not to say this is a flawless printer. There are some issues with the poor filament loading, and there are some users whose units had some questionable quality control. But overall, for this price point, the Ender 3 prints very well.
Pros
- Strong print-quality.
- Easy to get started printing.
- Inexpensive.
Cons
- Poor and unintuitive filament loading.
- Manual print-leveling only.
The best entry-level FDM printer
Original Prusa Mini+
The Original Prusa MINI+ is a big printer in a compact body with a low-midrange price point and strong performance. The MINI+ sits in the sweet spot where it can be a great choice for beginners to experts that might not be looking to spend too much on a printer. The Original Prusa Mini+ the next rung up from the Ender 3 in terms of entrance-level 3D printer. It is a compact, open-frame 3D printer that consistently produces superb-quality output for a great price. It requires assembly and calibration care, as well as shipping from Czechia, but that might be worth it for this printer in particular.
Like many midrange-and-cheaper 3D printers, the Original Prusa Mini+ is an open-frame printer that comes as a printer kit requires assembly, which sets up rather easily but might require some adjusting to get it running properly. The Prusa Mini+ is a bedslinging printer, which is common between many smaller, more accessible printers overall. Measuring 37cm x 33cm x 38cm (H/W/D), the Mini+ packs a lot into a small, desktop sized printer – with a footprint that is 40% smaller than the Prusa MK3S.The Mini+ boasts a 18cm x 18cm x 18cm build volume, which is a fairly large print volume when you consider its price and the similar bedslinger 3D printers available.
The print-bed, like with any bedslinger printer, is an important consideration, and Prusa demonstrated innovation with their design. The print-bed of the Prusa Mini+ is constructed with magnets, so it can easily snap on to print, and snap-off to pop the finished prints. A smooth PEI print sheet is included. All3dp noted the damage that the fingerprints can cause on the adhesive surfaced, but also noted the ease of removing the fingerprints with alcohol. The new SuperPINDA bed levelling probe improves the repeatability of your prints, meaning you can set up the probe after unboxing and print for a long time before ever thinking about the bed-leveling again.
The Mini features a standard 0.4mm nozzle designed for 1.75mm filament, that is ultimately replaceable in the situation of clogs and damage to the print nozzle. With this nozzle, this printer can create layers of between 0.05mm and 0.35mm, with a max speed of 200+ mm per second. The Hotend reaches temperatures between 100 Celsius and 280 Celsius, making this printer compatible with the majority of common filament materials, including PLA, PETG, ABS, and Flex. The Bowden tubing the filament feed has some issues – the filament sensors can only determine the presence of filament, not movement of filament, so blockages can still happen and prevent your print from completing. Fortunately, the company does a stellar job covering itself and its customers with helpful support channels, able to help you troubleshoot and replace components as you need.
Another area where this printer exceeds is in the controls that this unit offers. Prusa Research’s self-developed 32-bit “Buddy” mainboard, paired with TMC2209 stepper motor drivers, which allows for advanced features and quiet runtime, blowing many comparable 3D printers that only offer an 8-bit control board out of the water.
A 7-centimeter, full colour LCD display shows the options and settings on-screen, controllable by a knob on the front. The MINI+ comes standard with an ethernet port and optional future ESP Wi-Fi module upgrade which will enable sending files to the printer wirelessly. You can also connect via a USB to print as well.
The Mini+ comes with PrusaSlicer, Prusa’s own Slicer tech which is easy-to-use, with plenty of customizable options and material profiles. Combined the intuitiveness of PrusaSlicer with other quality of life like the automatic levelling, and you get a printer that goes from slicer to printing in next to no time.
Overall, the Prusa is a very strong option for new users or those without much space. It’s a strong printer for its size and price, although it is a little more expensive than the very comparable Ender 3 V2. If you are stuck between the two models, it breaks down like this: the Prusa model is more expensive, but offers a more thorough featureset including automatically bed leveling.
Pros
- Good features offered at its price point.
- Strong print quality.
- Strong auto-leveling.
Cons
- You could do more with a better extruder.
- No touchscreen controls.
The best desktop FDM printer
Original Prusa i3 MK3S+
We had to give the Original Prusa Mini+ one of the highest grades on this entire list. However, if the Mini+ impresses you, you might be even more impressed with the MK3S+. This mid-priced 3D printer is truly Original Prusa’s flagship and is the printer you should look at if your budget is one thousand or slightly more. While it only is a slight improvements on the MK3S, it is still the best mid level printer on the market.
The MK3S+ is available in a kit and as a preconstructed unit, with the kit being the more inexpensive choice. When constructed, the MK3S+ sits 50 by 56 by 38 centimeters (L/W/H) and should sit rigid and highly stable. The print bed is made from spring steel, with a PEI-coating that provides a maintenance-minimal print surface. The print area of this unit is 25 centimeters by 21 centimeters by 21 centimeters, which is a considerable size, especially compared to the 18 cubic centimeter size of the Original Prusa Mini+.
Printing with the MK3S+ is remarkably easy. A combination of a heated print-bed and a magnetic spring steel build plate make separating completed prints simple. Prusa offers three different print surfaces (smooth, textured, and satin) which mostly do not require separations of layers, or surface prep. The “+” here indicates a boost to the mesh bed leveling probe to meet Original Prusa’s standards. The MK3S+ features a SuperPINDA probe with a powerful sensor that automatically levels the Mesh Bed without fiddling around or risking uneven prints. The Mesh Bed Leveling is impressively easy to get a flawless first layer, even accommodating for imperfections of the print sheet imperceptible to the human eye.
The i3 MK3S+ is equipped with a custom E3D V6 hot end, extruding the filament through the BondTech dual gear filament feed – which all3dp.com notes are both household names in 3D printing. The hot end handles a majority of common materials of 1.75mm filament, including some common varieties including PLA, PETG, ASA, Polycarbonate and Polypropylene. The hot end heats the filament between 100 degrees Celsius and 300 degrees Celsius, however there is no enclosure to mitigate warping due to the cooler ambient temperature when printing at these higher temps. The filament sensor can detect the presence of filament inside the extruder, and can even detect colour, aiding precision on colour prints. The results of this printer are strong, with very few imperfections, which mostly tend to be loose filament. Fine detail is handled well, and overhangs do not sag and stay firmly in place.
The printer consists of a few main components: the base that supports the build plate, the arms, and the control panel complete with an LCD screen. The control centre is powered with an 8-bit Einsy Rambo mainboard, connected to a TMC2130 stepper motor drivers. The mainboard powers this unit’s sensorless homing “which sees the MK3S+ fling its print head and bed in the direction of home and registering the zero at the point it meets physical resistance. (In other words, the frame of the printer.”
Included is PrusaSlicer, an internally-developed Slicer suite that bears resemblance to Cura, with an easy learning-curve in the easier user level, with Advanced and Expert modes adding broader, more specific functionality.
Overall, the MK3S+, much like it’s little brother the Mini+, is a strong FDM printer that is both easy to use and well worth its money. However, the MK3S+ definitely shows up to Thanksgiving dinner in a new sports car just after Mini+ asked mom and dad for money – it’s that much more impressive. Where the extrusion is one of the weak spots for the Mini+, it’s one of the strong aspects of the MK3S+. If you have the money to spend and the desire for better printing, there’s really no reason not to upgrade to the Mini+.
Pros
- Real strong printing because of it’s impressive extrusion set-up.
- High-tech for your simplicity, not complexity.
Cons
- Loud.
- Expensive.
The fastest desktop FDM printer
AnyCubic Vyper
The AnyCubic Vyper is another bedslinging-style open frame printer that offers strong FDM 3D printing at a more affordable price tag. While there are many of this style of printers available, including some really strong offerings from competitors, AnyCubic has made a name for itself over the competition.
The AnyCubic Vyper is a printer that is available as a printer kit, so regardless, some assembly required. The Vyper measures approximately 50 by 46 by 51 centimeters overall and weighs 22 pounds, or just under 10kg. One of the differences the Vyper offers over other Ender style printers (including the Ender 3) is the build volume – 26cm x 24.5 x 24.5, (HWD) which is several centimeters larger than the Prusa Mini, (another Ender) and even the Prusa i3 MK3S+. Setting up the AnyCubic Vyper out of the box is simple compared to some of the printer kits that you can purchase. The instructions are clear, the tasks are clear and easy, and everything is labeled to prevent confusion.
the Anycubic Vyper is a bedslinging or Ender 3 style 3D printer, which describes how the printer prints in the three-axis – the Bed of the printer moves horizontally on one axis (often called the “Y-axis”), while the nozzle moves along the other horizontal axis and the vertical axis. These printers are ideal for beginners, since they are generally available at cheaper price, and offer open access to the mechanical components of the printer.
Like any bedslinger, the print bed is an important facet of this printer. The hefty print-bed is sturdy, with a textured PEI-coated surface and a magnetic design, your prints stick on to the print bed dependably, and then can easily pop off. The auto-bed leveling feature called “LeviQ” is fantastic, producing multiple prints while you might not even worry about the first layer. The rough-textured PEI print bed offers convenient print handling, but we maintain that it obliviates any fine detail you might be trying to achieve with your first layers.
The Vyper includes a bevy of notable features that are designed to produce strong prints. These include a dual-geared extruder and tall nozzles with extended melt-zones, improving the flowrate of filament through the hot end. A filament sensor sits inline before the extruder, ensuring extrusion goes off without a hitch. The filament sits on a spool holder supported by desk, attached on the side. Yes, it makes the footprint of this printer effectively larger, but you will not have difficulties feeding the extruder. The Vyper is compatible with a wide variety of materials, including PETG, as well as the standards like PLA, ABS, although noting that this printer is not enclosed does limit the effectiveness of printing some of said materials.
When it comes to the components and parts of the Anycubic Vyper, we were impressed. Figuring out the user interface is remarkably easy – the layout is well-thought out, and the onboard monochrome touch LCD screen is more intuitive than the knobs we are used to with other desktop FDM printers. The 32-bit Anycubic mainboard with TCM2209 steeper motor drivers prove a competent combination to run the printer on. We like that the Vyper has a slot for a full-sized SD card and USB connection – enabling offline printing, as well as means to control the printer via OctoPrint.
Buying the Anycubic Vyper comes with a copy of Ultimaker Cura as slicing software, which is a sweet deal since Cura is so renowned among 3D printer afficionados. Unfortunately, this Cura copy does not have a custom printer profiles for the Vyper, and you will need to customize the profile for the Anycubic i3 instead. “But don’t worry, this process is described in the instructions!” I say, sarcastically. Even after customized, this setup can respond slowly to start G-Code. It would be such an easy thing to amend.
Users overall found that the Anycubic Vyper produced very high-quality prints. This printer’s strong movement of filament means it is a speedy little printer, but it is not as fast as a CoreXY or a delta-style printer. While the print performance and quality are generally great, certain prints with precise tolerances can be difficult to dial-in exactly. The textured yet smooth coating on the print bed is designed to secure prints more effectively, however this surface does not offer improvements over glass for printing many materials. If there is residue or residual print left on the PEI coating, be careful when scraping the print bed, as this texture might come off.
Pros
- Prints fast for it’s style of printer.
- Easily removable print bed with automatic bed leveling.
Cons
- Print bed prone to limiting detail on the first level and even chipping.
The best FDM printer on the market
Ultimaker S5 & Ultimaker S5 Pro Bundle
Okay, so we have covered a fair number of 3D printers that offer some impressive features while not breaking the bank. But these models are almost exclusively designed for hobbyist use. If you require commercial 3D printing, whether designing prototypes, equipment parts or printing large quantities of prints, then you will need to spring for a powerhouse of a printer. For an FDM printer built for professional use, we can safely recommend either the Ultimaker S5 or the Ultimaker S5 Pro Bundle for you.
For starters, even just by looking at the machine and its large stature informs you are not just dealing with a starter-printer. The Ultimaker S5 is a decent sized unit, with a blocky shape (unlike the skeletal frames of many other FDM printers) with measurements of 49.5 x 58.5 x 78 cm (LxWxH). This size comes with advantages, especially in the build volume, which has dimensions of 33 x 24 x 30 cm, which is overall a decent print size. Where the Ultimaker gets huge is with the Pro Bundle, which adds a wide variety of features to the mix (like air filtering and material handling) – bringing the height of the Pro Bundle to 1.1m tall.
The S5 is a powerful FDM printer. With excellent dual-extrusion 3D printing, you can print in multiple materials, adding an impressive amount of material flexibility with your prints. The print core technology in the S5 is unique to Ultimaker, using interchangeable hot ends that cleanly snap into place whenever you need to change materials or process between or during prints. Considering some printers require you breaking out the tools to do the same, we give points to the S5 in this regard. The print bed is constructed of glass, is removable, and is temperature controlled to temperatures of 140 degrees Celsius. While glass is a decent print bed material, certain materials are not the best with it, fusing with the first layers of some thermoplastics. The print bed automatically levels, which of course is expected at this price range.
The S5 has two print core bays, each compatible with one of three different cores that the Ultimaker is compatible with. The codes AA, BB, or CC, codes separate the thermoplasters as “AA” (like PLA and TPU), polyvinylalcohol (PVA) water soluble materials as “BB”, and then composite materials that would ruin the other core’s nozzles are coded as “CC”. Each core will digitally communicate to the printer, so the printer knows which material it is prepared to print, alerting the user and avoiding failure if components of the printer are not quite adding up. There are a wide range of filament you can use with this printer, granted it works with 280C maximum hot end temp and 140 degrees Celsius max heat bed temperature. Although, non-Ultimaker produced materials can be harder to get the machine to recognize
Let’s go back to the additional features included in the Pro Bundle. Among the facets of the Pro Bundle that give it its extra height, the biggest inclusions are the Material Station, and Air Manager. Ultimaker’s Material Station – lets you load up to six spools of material, switching or reloading when necessary without you needing to worry about it. The air manager unit provides a temperature-controlled and particle-free environment by use of a HEPA filter to ensure outside factors do not negatively impact your prints.
Like many of the more premium 3D printers, many of the controls and diagnostics are accessible through the touch screen on the front of the unit. You can connect the printer to internet through a local wireless connection or through Ethernet. A USB port can let you physically send files to the S5 too.
The slicing software most compatible with the S5 is Cura, which is actually maintained by Ultimaker themselves. Being optimized for the most common slicing software is always going to feel nice. Another software included is Digital Factory, a cloud-based platform designed to help you manage projects and print-queuing. One thing we noted is that Ultimaker S5 is not as friendly to materials that are not created by themselves. While there is a selection of third-party materials designed to work with the S5 as part of Ultimaker’s Material Alliance, using these require you to download the material profile from Ultimaker Marketplace. While the software with the S5 synchronizes automatically, the hardware included in the Pro Bundle doesn’t. You need a local connection exclusively to synchronize to the hardware, and until you do that, Cura will not let you use the material until you do this. All3dp stated that newer machines can load printer material profiles from USB for a slightly easier workaround, but idealistically that’s still too unwieldy.
While both the S5 and S5 Pro Bundle share base tech together, it is very important that these two units are not seen as interchangeable, since there is clear difference between their intended uses. The S5 is a strong base, and one that professionals to ultra-hobbyists alike can get good use for. It’s not too big, is overall easy to use and set-up. The Pro-Bundle adds some significant bonuses in the Material Station and Air Manager, but since not all uses or materials will require these features, it’s not worth the extra money for everyone to get these features while also increasing how complex the machines are. If you require regular 3D printing at your work, and are gravitating towards fused deposition modeling over stereolithography, then this printer is worth a long consideration.
Pros
- Easy-to-use, efficient design.
- Tools designed for business use like always-on functionality and reporting.
- Very automated – you do not need to do much while you are printing.
Cons
- Extremely expensive for both models.
- Glass print bed can chip and Ultimaker does not offer an alternative.
The best desktop resin printer
Elegoo Saturn 2
Resin printers offer their own benefits that make for excellent printers for creating fine detail and structurally sound prints. The Elegoo Saturn 2 is a resin 3D printer that proves a strong alternative for a midrange level printer, due to its mid-sized stature and mid-priced cost. Don’t be fooled – there’s nothing mid about its performance.
The Elegoo Saturn resembles a rectangular siren light, with a taller, slimmer design than many other 3D printers. The dark red acrylic hood covers the functioning parts, protecting them and keeping fumes from the curing process of filament. The dimensions of the frame is 30 x 27.3 x 56.7 centimeters, and weighs 11 kg. The build volume of 21.9 x 12.3 x 25 centimeters is larger than the previous Saturn, which you can never complain about.
The Saturn 2 offers a printer resolution of just 28.5 microns, which is made possible by an impressive 8k screen. Yes, it’s fancy, but it includes a screen protector so you do not need to worry. This level of resolution makes even the most detailed prints possible, even on larger builds.
The Elegoo Saturn features a Fresnel lens beneath the LCD and above the UV light source, designed to control where the UV light will emit. This lens, combined with an Array of 64 UV LEDs, allows for amazing light uniformity – 92% which improves the precision possible with this printer. However, like all3dp noted, the fact that this light system is permanently installed under the hood means components are inaccessible for repairs.
Resin printers are known to produce some fumes, so Elegoo included an air filtration system to keep your home safe and odour free. The Elegoo solution is an activated carbon filter that is replaceable and USB powered, with it’s own dedicated USB port so each feature (like the USB printing) is not competing for the same points. While we appreciate the inclusion, users noted that the unit did have some faint traces of odour from the resin, meaning that the filter is not full-proof. Users should consider finding other ways to protect themselves or their families, whether via ventilation, use of PPE, or doing your printing away from others. The Saturn 2 includes a vent for an external ventilation system, which is easy to cover up.
You can control this printer through the Monochrome LCD screen, or through your computer, as you wish. The printer has a USB port at the side of the unit, which enables printing through the USB. The Saturn 2 includes a copy of the software ChiTuBox, a slicer program with an emphasis on SLA and DLP style prints. Elegoo does not offer different presets available for their different resins – just a base resin profile. This means that each resin – both third-party resins and resins from Elegoo themselves have the same profile. The results of this profile across the different resins seems to do alright, but having the ideal settings dialed in automatically with a resin presets would make the Saturn 2 much easier for printing with. Printing with the Saturn 2 is fine, but seeing omissions like this, newcomers could find better types of printers that are more easily optimized.
Overall, users have shared their enthusiasm for the prints of the Saturn 2, combining excellent 8K print resolution with a larger build volume. It’s easy to set-up and not hard to use, and the fact that you can get a quality resin printer for desktop use is a huge boon. However, some notable omissions (like the printer profiles) are legitimate detractions about this printer. While it’s not perfect, it’s the best desktop-resin printer for its price.
Pros
- Strong resin printer that can fit on your desktop.
- Due to the inherent advantages of resin prints, you can achieve intense detail.
Cons
- Light technology inaccessible for repairs or troubleshooting
- Lack of resin profiles.
The best resin printer on the market
Formlabs Form 3
The Formlabs Form 3 makes other 3D printers jealous when you bring it up in conversation. While it is expensive, it offers impeccable features and excellent printing, at a desktop size, while never feeling overwhelmingly difficult or fiddly to work with. For professional engineers and designers, or even just hardcore 3D printing enthusiasts, this is truly a printer that is hard to beat.
The Form 3 looks like most Resin printers, albeit larger, with the mechanisms of the printer in the base of the machine, and a transparent orange hood that flips open via a hinge. The hood is composed of an orange plastic that blocks UV light from escaping, so you can watch the progress of your print without outside light interfering with the curing process. The Form 3 has a footprint of 40 cm x 37.5 cm x 53 cm, which makes the Form 3 a decent choice for those who are limited in space. With a print area of 14.4 x 14.4 x 18.5 cm, you can create a wide range of structures and objects of different sizes. Too small? Formlabs offers a The Form 3L with a build volume of 29.9 x 33.5 x 20 cm build size at a much larger stature and price.
The difference in prints you can achieve between an FDM-style printer and an SLA-style printer is considerable. Resin-style printers are capable of a lot more in terms of exact detail, strong surface finish, and higher-quality components than other extrusion processes. A lot of these qualities come from the unique process of stereolithography. New to the Formlabs Form 3 is an all-new Light Processing Unit, which unlike many other SLA style printers, features a laser that moves along the X and Y axis, ensuring the laser hits the resin perpendicular to the print surface, improving detail and scalability in use. Another innovation included in this printer is what Formlabs calls “Low Force Stereolithography”, where the printer starts at the top of the print and the hardened plastic is elevated up, instead of the print starting at the bottom and being built-up.
Despite some advanced sounding technology and processes that happen inside when the enclosure is closed, the Form 3 is one of the easiest 3D printers to use, without needing to fiddle with components or settings too much. For starters, the resin vats are entirely modular and disposable – refilling resin will not mean you will need to work with the gross, somewhat toxic resin directly. Other automations like automatic build-plate levelling are very valuable to the ease of operating this printer.To keep the use of the Form 3 simple, Formlabs outfitted this printer top to bottom with sensors that detect if any problems arise during printing and can offer diagnostics. Formlabs backs this printer with their strong customer service, proving Formlabs really stands behind their product.
The Form 3 is controlled by a touch screen interface that you can use to directly control the print, including setting up the printer and starting or stopping prints. Of course, the included PreForm software and the online printing dashboard are better suited to control the more detailed aspects of your printer. You can connect via WiFi or Ethernet port included in the back of the printer.
Let’s get back to the software. The aforementioned included PreForm software manages print preparation and monitoring of your prints. Available for free for either Mac and Windows, we are happy to see that PreForm is more than just a slicer designed for the Form 3, but instead a well-thought out offering that is easy to understand, while also being perfect for the Form 3. There is also the Printing Dashboard – an online service that manages the prints from the Form 3. It’s aimed more at users who operate multiple Form printers or share one printer among many, so unless you have one or several Form 3’s for the workplace, you might not need to worry about this service.
Overall, it’s very clear that in terms of not just SLA-style printers, but 3D printers in general, the Form 3 stands out over the others. Just the sheer level of detail we have seen possible with the Form 3 puts it square into the upper strata. However, the cartridge-style resins make refilling your resin easier, and the expansive amount of sensors keep everything running smoothly. It’s the type of machine you can learn how to work after some quick study, or delve deep into to see the possibilities that exist with it.
Pros
- Super easy.
- Extremely impressive results.
- Strapped with sensors so you know when things are not quite right.
Cons
- Resin cartridges are wasteful
- Woah – that price.
Frequently asked questions about 3D printing
What is a 3d printer?
A device used in the process of 3D printing or additive manufacturing, which is a where you can create objects in three-dimensions out of a variety of plastic materials to the specifications of a digital file.
How does a 3D printer work?
Across the board, 3D printers work by using a kind of printing material, which the printer structures and organizes according to the programmed instructions, where the material will set and become hard plastic. This process has some variations based on the type of 3D printer you have. FDM printers utilize a plastic filament which is heated before extrusion and cools after application, where SLA printers utilize a liquid resin that when hit with the printer’s laser, is transformed chemically into a hard plastic.
The process of you starting a print starts with a 3D model, which is programmed in either some 3D modeling software or computer-aided design software. Tinkercad, Fusion 360, and Blender are some modelling software that you can consider using with your 3D printer. Of course, you do not need to design your own models to use a 3D printer – there’s a marketplace of files to print online, including such sites as Thingiverse, MyMiniFactory and Printables, with many such prints on these sites being free.
You will also need a slicer – a piece of software that converts the models into instructions for the 3D printer. Your printer will likely have its own slicing software, but if it does not, Cura is always a strong place to look for a trusted slicer among many. After you selected a model and loaded it into a slicer program, you should be ready to start the 3D printing process.
How much is a 3D Printer?
3D printing had been prohibitively expensive until the RepRap movement, where hobbyists sought to make a 3D printer capable of printing the components of a complete 3D printer. From these hobbyists arose the always-evolving world of modern 3D printing, where you can find a simplistic bedslinger for a couple hundred dollars Canadian, or find an advanced printer designed for professional use for upwards of ten thousand dollars Canadian.
Where to buy 3D printer?
You can buy a 3D printer at stores that carries the latest electronics – like Best Buy and Staples. However, many of these printers are available on Amazon, dedicated 3D printing storefronts like https://spool3d.ca/ or the company’s own website, which may offer more competitive prices, warranties, or support.
What can you make with a 3D printer?
3D printers are so exciting because they can create such a wide range of shapes, and transport ideas from the realm of the immaterial to the material. In general, a 3D printer can create solid objects of almost any shape in three dimensions with some caveats.
However, the reality of what you can print comes down to what you can design yourself on a slicer or what you can source online that someone else has designed.
What material does a 3D printer use?
3D printers often create their 3D shapes out of various kinds of plastic material. How printers may create the plastic depends on the type of printer.
A filament printer will melt the plastic material to a state where the plastic becomes fluidic, whereas a resin printer uses the process of stereolithography to chemically alter the resin into a hard plastic material. There are other non-filament materials that certain 3D printers can use to print their models, however some of these printers are more designed for non-hobby, industrial use.
What is the purpose of a 3D printer’s heated bed?
A heat-bed adds additional control over parameters related to the temperature of the print-bed, or the base where the 3D print is created upon. Controlling the heat of the print bed improves adhesion to the print bed, improves the adhesion between layers, and prevents runaways and warping of the material.
How to clean a 3D printer bed.
The 3D printer bed is truly an important component for quality in a 3D printer. However, after several prints, the worksurface of the printer bed might become covered in filament and such creating a strong adhesion to the surface might be harder to achieve. Keeping your 3D printer bed clean helps with this greatly.
First, think about what material your print-bed is made from, since different materials will call for different methods of cleaning. The most common constructions include glass, adhesive tape, or PEI sheets.
PEI: Unscented isopropyl alcohol, added to a cloth or paper towel, can easily scrub out PEI sheets – just let the printer bed cool down before you clean.
Adhesive Tape: Gentle scrape the material, since it’s delicate, or replace it.
Glass: Use a scraper to remove the dried-on filament from the bed.
How to clean 3D printer nozzle?
Just like your print bed, other components of a 3D printer will need cleaning if they begin to accumulate material. Especially with FDM 3D printers, where the nozzle heats up hot filament and deposits it on the print, excess filament can easily cause problems regarding the functionality and print quality of your printer.
To clean a 3D printer, first you should look out for common issues, like the nozzle not layering filament, which is indicative of jams.
To clean external debris: Wipe down the exterior of your nozzle using cloth or alcohol wipe while the nozzle is still hot, being careful not to burn your fingers.
To deal with the ever-common clogs in your nozzle: you need to remove the clog somehow – whether that is by using a small needle to break-down the clogged filament, or attempt a “cold pull,” – a technique using your filament strands and strategic heating. If neither technique works for you in this situation, you can try taking the nozzle apart if your nozzle lets you, or replace the part.
How to make money with a 3D printer?
3D printing as a hobby can be a fun way to flex your creativity and create anything you set your mind (and printer settings) to. However, some turn to 3D printing as a way to make some money.
It makes some sense: 3D printers have a high initial cost and some level of a learning curve, so there are some obstacles of entry, but the actual costs to run a 3D printer once you own one and figure it out can be super inexpensive. So it makes sense for many to try to get into a 3D printing business, or try to monetize your hobby just a little. Here are some tips to think about before you purchase.
- Identify what service or goods you will offer. Having a niche will help you separate yourself from other individuals or companies that offer 3D printing services.
- Get your process and skills to the point you are confident in producing whatever a customer may want from your business. Hone your craft so you do not get unhappy customers.
- Build a following! Social media can be a great place to reach out to hobbyists or professionals who may choose to use your services.
When was the 3D printer invented?
While 3D printing has been a novel concept for a long time, the tech has been around for a while. In 1981, a researcher named Hideo Kodama (not the politician) developed a device that manufactured prototypes layer-by-layer, using a photosensitive resin that was polymerized using UV light. This machine is arguably the first SLA type 3D printer ever developed. Unfortunately, Kodama’s inabibility to secure a patent meant his part of the 3D printer story end there.
Instead, in 1986, an American furniture maker named Charles Hull was able to secure a patent for his model-making machine that utilized a photosensitive resin was able to secure a patent and soon, Hull’s company 3D Systems Corporation released the first commercial device that could be described as a 3D printer: the SLA-1 in 1988.
However, the ball really started rolling for modern 3D printing in 2005, when Dr. Adrian Bowyer created “The RepRap Project,” an open-source initiative to create a self-replicating 3D printer, down to replicating each of its own components. From there, 3D printing began hitting more and more milestones, as the technology became more known and understood. The 2010’s saw prices of individual units drop, becoming available to the general public, while the tech inside became easier and better.
Read more
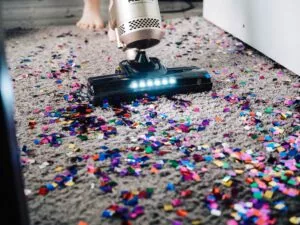
The Best Vacuums in Canada
Vacuum cleaners are great. The problem? There are too many out there.
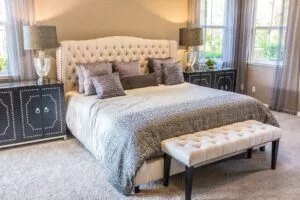
The Best Duvets in Canada
Find here the best duvets to bundle up in winter.
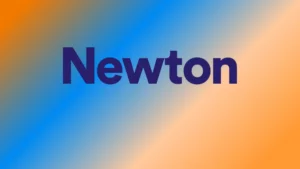
Newton Review: Features, Trading, Pros and Cons
Newton is a Canadian crypto exchange. Check out this article to learn more.
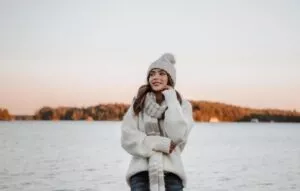
Things Danya Hasan Can’t Live Without
Here’s everything the Canadian influencer carries in her bag.